The tractor manufacturing behemoth from Mohali adheres to the RRR model, which stands for Recycle, Reduce, and Recharge. Let’s now understand the certifications that Swaraj Tractors have managed to get over the past few years – and how they did it.
Zero-waste-to-landfill (ZWL) certification
The primary goal of Zero Waste to Landfill (ZWL) is to generate zero waste/trash that will be sent to landfills, incinerators, or the ocean. When an organisation diverts 99% of its waste from landfills, it achieves the gold standard in ZWL.
Waste reduction initiatives of Swaraj Tractors.
The company has managed to divert 99.998% of its waste from landfills. Here’s how they did it:
- Installed a solvent recovery system in the paint shop to reduce thinner consumption
- Use of electrostatic guns for direct paint reduction
- Recycling of transmission oil
- Coolant sump life improvement in the machine shop
- Zero leakage initiatives across plants
- Use of efficient sludge filter presses
- Recyclable packaging for different tractor parts
- 3 bin system in place on the shopfloor
- Reduce paper use and recycle
EP-100 certification
EP100 is a corporate commitment platform through which companies pledge to improve their energy productivity by deploying energy-efficient technologies and practices. By joining EP100, companies commit to reducing their energy consumption in relation to their economic output, ensuring that they are maximising their economic and financial gain from the energy that they use.
Energy efficiency initiatives of Swaraj Tractors
Swaraj division achieved 101% energy productivity. Here’s how they did it:
- Operating both plants at peak efficiency
- Air wastage elimination
- Installed additional air receivers to improve air quality, thereby reducing compressor load and power consumption
- Dedicated compressors for HT and tractor rework area
- Night shift power wastage elimination
- Variable Frequency Drives in all paint shop motors
- Installed electronically communicated motors
- Optimum running of PTCED pumps during pre-start up
- Conventional fans on the shopfloor replaced by BLDC fans
- Conventional ACs replaced with energy efficient ACs
- Solar panels of 460KWP capacity installation
- Machine peripherals automatically switch OFF when the machine is idle for more than 10 minutes
- Heat loss reduction in the paint shop and process optimisation.
- Waste heat recovery from the air compressor to heat chassis pre-treatment stages
Water positivity certification
When companies replenish more water than they use, they become water-positive.
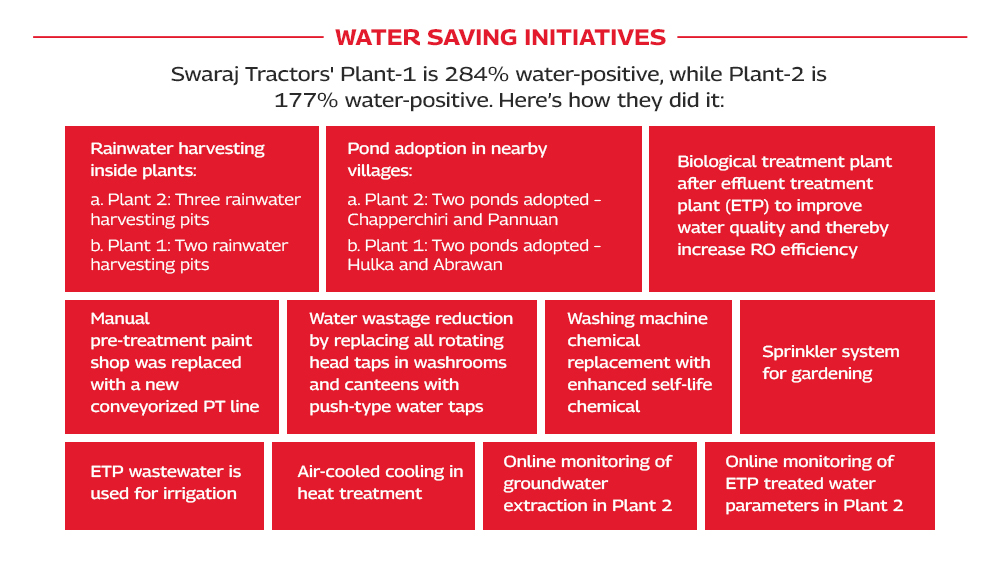
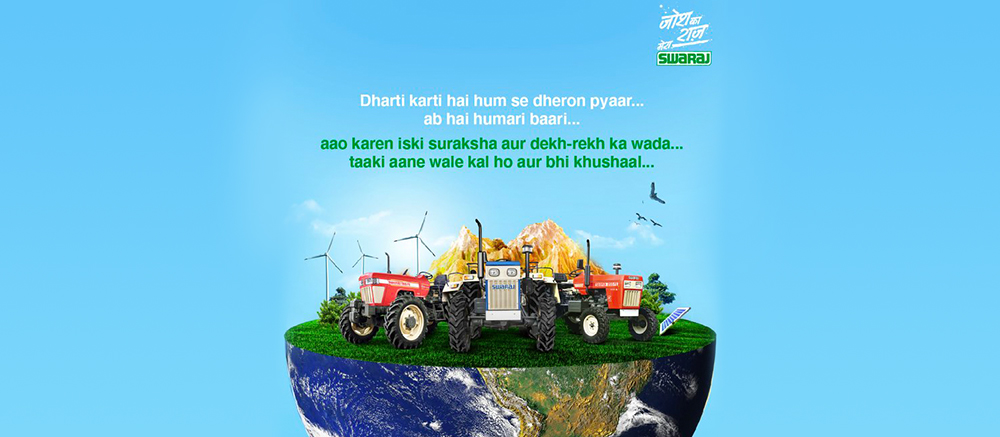
You can also share your thoughts in the Comments section below!